Acoustic solutions
TRAKETCH® Membranes for the protection and optimization of sound quality


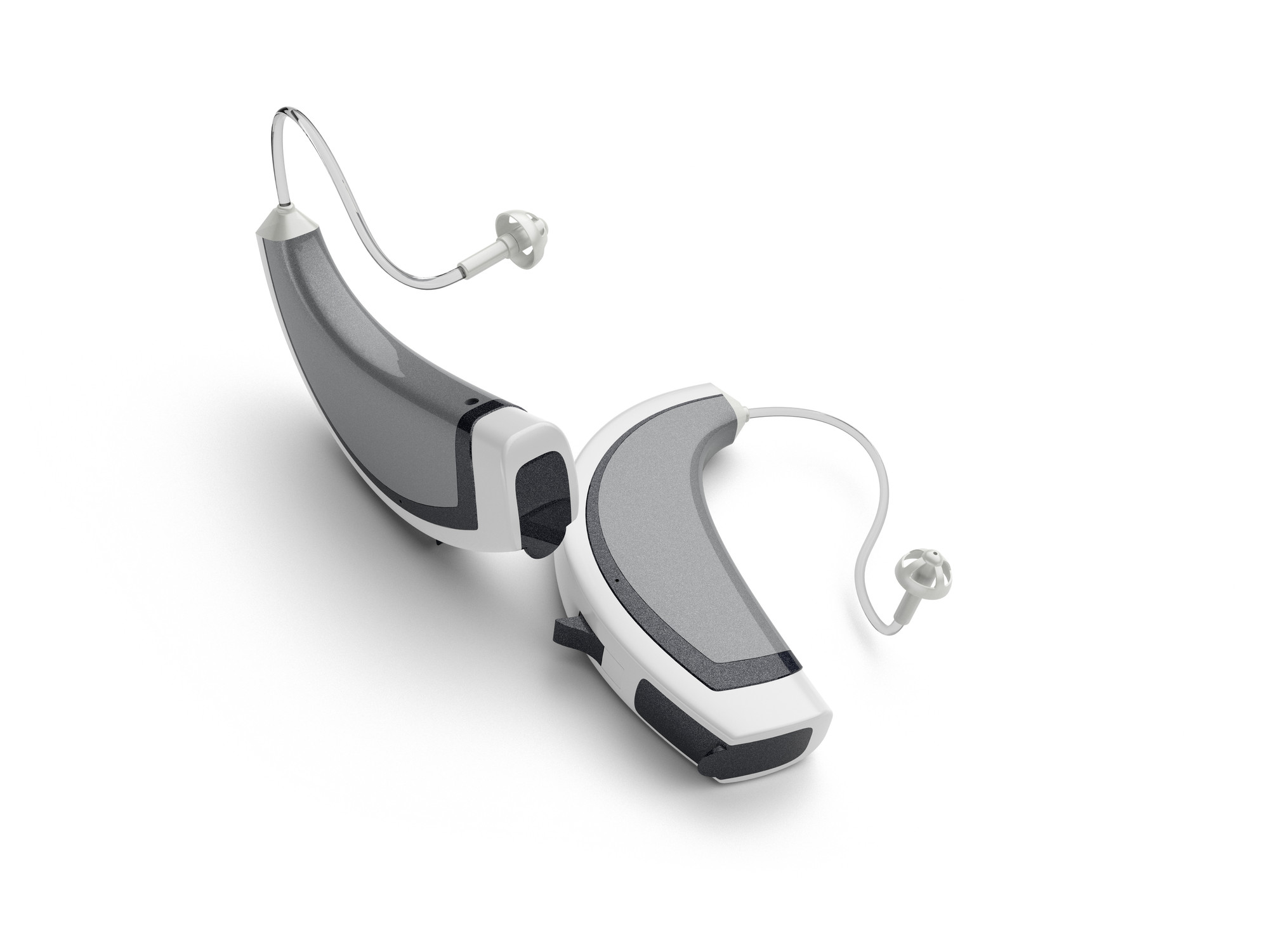
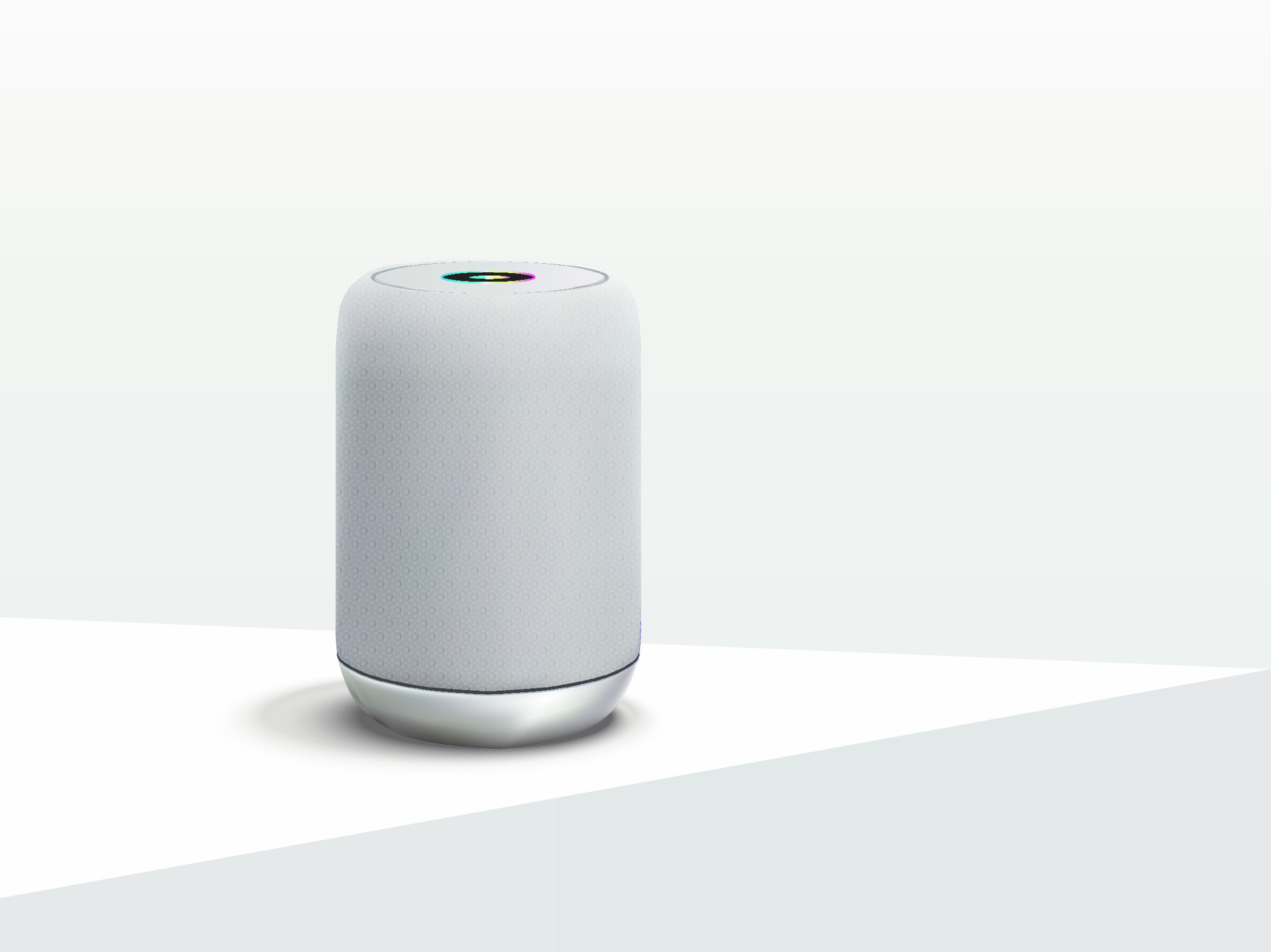
The challenges today’s acoustic product solutions have to meet is inherent in the protection of highly sensitive electronics against dust and liquids and to simultaneously prevent negative effects on the acoustic properties.
The use of our microporous TRAKETCH® Filter Membranes (PFOA/PFCA-free & PFAS-free upon request), the cylindrical pores of which can be perfectly size adjusted during the manufactur-ing process, puts us in a position to guarantee the concise achievement of this goal. TRAKETCH® Filter Membranes preserve the application specific sound quality / transparency, including all acoustic properties. At the same time, they protect sensitive electronics, such as loudspeakers and microphones against external impact.
Our product portfolio ranges from membranes on rolls to preassembled membrane components to the development of complex component groups in combination with plastic injection molds.
Product solutions and configurations
Injection molding and filtration are our passion. In these areas we develop products based on customer specifications, manufacture serial products and resolve current challenges to offer best solutions. To that end, we partner with you from the start in the development process from the initial idea to the series production of your component.
- Membranes on rolls
- Preassembled membranes
- TRAKETCH® adhesiveVENTpads
- Injection molded membrane parts
- Complex components and component groups
- Shape-related standard products under our off-the-shelf FLUXX® brand.
For additional information visit FLUXX® Degassing Inserts
Application examples
- Electronic earmuffs or heating aids
- Microphones and loudspeaker systems (also for outdoor use)
- Two-way speaker systems and radio devices
- Mobile and portable devices, such as smartphones, tablets, cameras, smartwatches and headphones
Your contact person
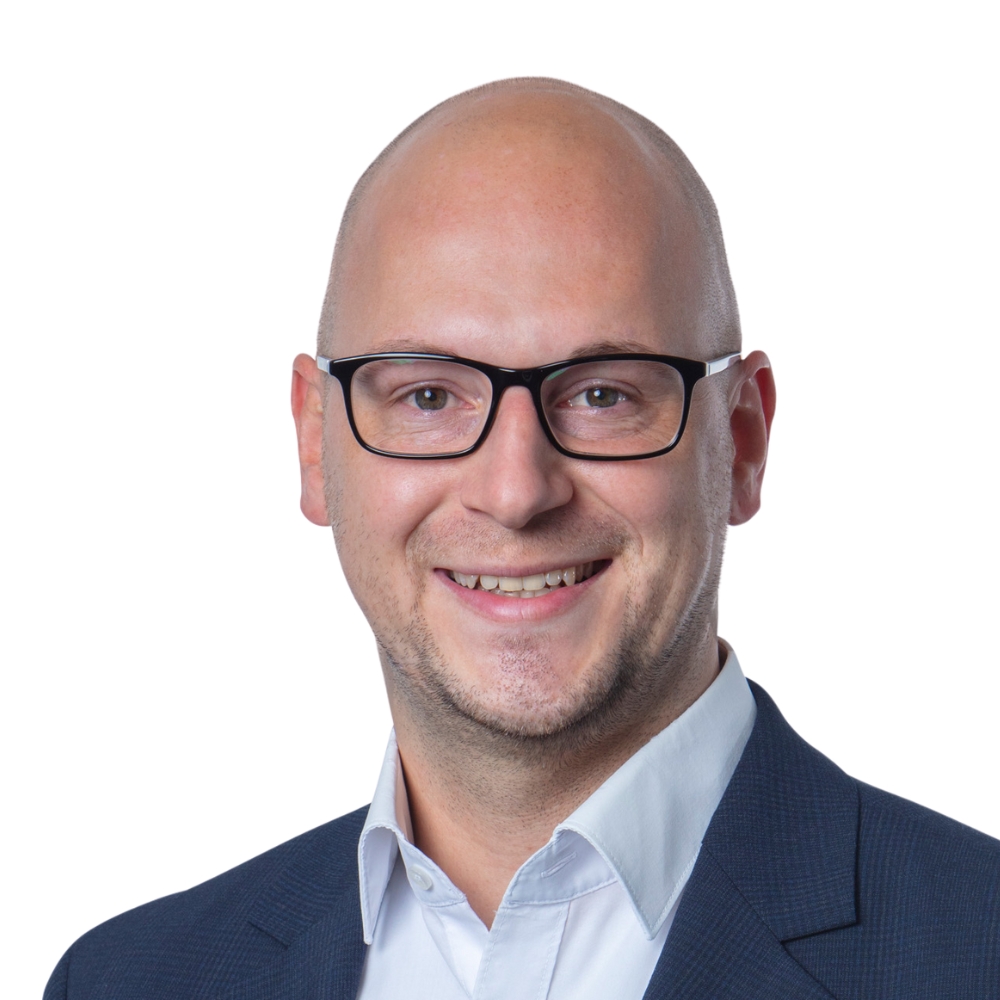
Kevin Eckert
Head of FLUXX
Packaging & Industrial